Building Morbic 12
by Martin Chambers
The year 2020 seemed like as good as year as any to build myself a small sailing dinghy. The idea began when my brother gave me a model boat during two weeks isolation, and after I completed it I thought ‘Why not make a real one?’.
Although the seed was probably there from early days as we spend most of our lives trying to rediscover the simple joys of our youth, in my case messing around in boats. I eventually chose the Morbic 12, a very pretty sailing and rowing dinghy designed by French naval architect Francois Vivier. I think it is the boat used in the film of Swallows and Amazons, so it was an obvious choice.
The Morbic 12 kit
O’Connor Wooden Boats uses a CNC machine to cut the plywood and supplies the boat as a kit. All you do is the final cut out of the bits, glue them together and slap on a coat of varnish. Simple.
The Morbic 12 kit
Well, it is simple in that most tasks are straightforward and the plans and instructions supplied by Vivier are comprehensive and the kit makes it all pretty obvious. But my boat is not perfect and if I built a second one it would be better. So if you wanted to build something similar perhaps you can learn from what I did.
Assembly of building frame.
Strongbox and building frames
The building frame is supplied as part of the CNC kit. The final boat will be accurate, as in symmetrical and straight, only to the extent you have taken care to measure and assemble this frame accurately. A trap here is that the plan measures the position of each frame on the strongbox from a reference of the previous frame, sometimes from the front face and sometimes the back. It is imperative the bulkheads and frames as shown in the picture are exact and square.
Pencil line
Tony O’Connor, owner of O’Connor Wooden Boats, was very helpful and suggested to both glue and screw these frames in place as the frame plywood is cheap stuff and construction loads might distort an inadequately solid frame. I had some trouble with setting the frames in place and figured I might need to adjust them along the way, so I elected not to glue. The picture shows the story, a 6mm error in pencil lines. Luckily, pencil lines can be sanded out and anyway symmetry is very overrated in small boats.
Making the stem and false stem
Gluing the false stem
Before you start making the hull you will need to make the transom and the stem, and you will need the stem as a mold to shape the false stem on. This is a job requiring more hands and clamps than you own. Wood for the false stem does not come with the kit and laminating the false stem is time consuming, but the hull work cannot begin until it is done. Vivier specifies laminating it from solid wood strips but I elected to use ten layers of 3mm marine ply. This seems to have worked well.
Centreboard, rudder, centreboard case.
Rudder assembly
Centreboard case
While waiting for the successive layers of glue to dry on the false stem you can get on with some of the other items. The plans call for two mast cleats that I chose to manufacture from hardwood. Also in these pictures you will see the sampson post and thole boards that you will see reappear in subsequent photos. The tiller is five laminated layers of Oregon.
The centreboard case in particular is another item that will require several days to make, unless you cheat and use fast setting epoxy. The plans are a little vague here, I elected to screw and glue the construction. Seal it well. Once assembled, there is no way to get inside to fix errors or leaks. This is another thing not to hurry. Remind yourself, the joy is in the process as much as the finished product.
One thing Vivier does correctly state is you need space. You need room to lay out the boards, to glue things together, to shave mast and spars. It would be possible to do the entire construction in the space of a standard carport, but jobs would have to wait until the previous task was finished.
Sampson post, thole boards
Lucky I could park our cars on the street so I had the luxury of space. You might also notice a lot of books in some of the photos, but no, I did not build it in the living room. We just have a lot of books in our garage.
Hardwood cleats
The tiller
Spars: mast, yard, boom.
There are three sail plans to choose from. I chose the Lug Sloop. This shifts the mast a little to the rear and you lose space for a forward rowing thwart, but you do get a bowsprit and I thought that was pretty cool. I elected to use Oregon, (timber for the spars is not part of the kit) in the process turning most of it into woodshavings. The plans give no instruction on how to achieve a tapered round spar from a square of laminated timber, but google and youtube help. If I did it again I’d go to the trouble of a hollow mast as the solid core one is quite heavy.
Laminated mast blank
Sequence is, make taper, make hexagon, make round. Simple.
Laying the planks
On the building frame you have installed bulkheads, the transom and the stem. Now at last you are ready to lay the planks and in this regard the building instructions are clear. Each plank comes as two pieces with a puzzle join so you must assemble them but it is not really much of a puzzle. The instructions call for a fibreglass patch over the join, and I suggest you use a very fine weave glass cloth so it will not show in the final construction.
Puzzle joins on the planks
I found it efficient to glue a board onto the hull, and with the same pot of epoxy, glue the next puzzle join. I used a total of six litres of epoxy but it would be very easy to be wasteful. The process is : mix epoxy and decant a little to mix with TPDRA to make a timber sealer to wet the edges of the plank to be installed. Then cover the glue surfaces with epoxy, then mix a high strength filler with the epoxy to form a glue that becomes the third layer. Assemble the board and clamp in place. Leftover epoxy is used to seal plywood or glue the next pieces, and as a filler in the gap left between the clinker edge of previous boards.
Gluing the sole
The CNC cutting creates accurate strakes so there is no need for trimming, but there is the need to scarfe and shape the ends. The bow chamfer needs to be about 30cm long and this is explained in the instructions. An edge plane is the tool you need, although I often reverted to hand plane and chisel only because I knew better how to use them — the best tools in the hands of a fool, etc. At the transom where the curve is greater the plan suggests an option of cutting notches in the transom. I didn’t do this but I think it would be a neater way. The desired effect is to have the clinker overlap disappear at the stem and stern.
Wood battens to hold plank in place and prevent bruising
The plan suggests temporary screws but I found I could clamp the boards in place. My personal best was 18 clamps to hold one of the strakes while waiting for the glue to set. This is the reason you can only fix one strake at a time. I did it this way as I wanted a varnish finish to the final boat and hence no screw holes.
Another learning experience I did not make until too late was that epoxy will run between the boards and leave dribbles along the inside of the hull. As the hull is upside down you will not see these until later. They can be removed with a heat gun and scraper, but it is a lot of extra work. I suggest you support the strong box and building frame up off the floor so you can get underneath to tidy as you glue each plank.
Glue runs
Of course if you elect a painted finish a lot of this will not matter. Paint can hide a multitude of sins.
The interior
After the last strake, called the whiskey strake, you can turn the boat to construct the interior. If you paid attention at the beginning and used plastic over the building frame, the hull will lift off the frames with no difficulty. I used leftover bits from the kit to make a cradle, and we had a small party to celebrate even though the boat is not yet half done.
Turning party
Vivier instructs that the hull at this stage can be pulled into shape with ropes. Maybe easier said than done. Take care to trim the side seats as these form the waterproof buoyancy tanks so need to be a good fit. I used copious amounts of epoxy filler to ensure a good seal, and weighed them down to glue them in place.
Clamps, weights, anything to hold it until the glue sets
Tony O’Connor suggests that boat building is a series of problems to solve, and I think he is right. Such as, the plan calls for an eyelet in the bow to attach the bobstay to, but to install it requires drilling end on through the single sheet of the stem ply.
Or, the brass keel strip is screwed to the hull on the exterior, but in the bow there is nothing to screw to other than a single layer of ply. I attached a fore keel to solve this problem, shaped from a 40mm by 20mm piece of hardwood (Tasmanian Oak).
Other departures from the plan
Vivier warns builders not to depart for fear of weakening the hull or overloading it. But in many small areas I departed his plan. Often, this was because I already had something close to what was needed. A small turnbuckle on the bobstay rather than a purchase. The mast is lashed in place to the sampson post, and the cleats for halyards are on the mast rather than belaying pins on the foredeck. I used ply for the skeg rather than hardwood. Also, I had some rather nice brass rowlocks from my father so I have installed these and will be using standard oars that I also inherited from my father.
To hide the fact this is a plywood epoxy and not a genuine timber boat, I used copper nails and rivets on the gunwales.
Copper rivets on gunwales
One departure you might notice from the pictures is I did not install inspection ports on any of the sealed tanks. If I need to I can do this later, but I didn’t like the look of those white plastic things. Also, I did not see the point of a transom drain plug.
I manufactured a yard collar from aluminium flat bar and leather, and from Classic Boat Supplies in Sydney I found Hemp lookalike polypropylene rope.
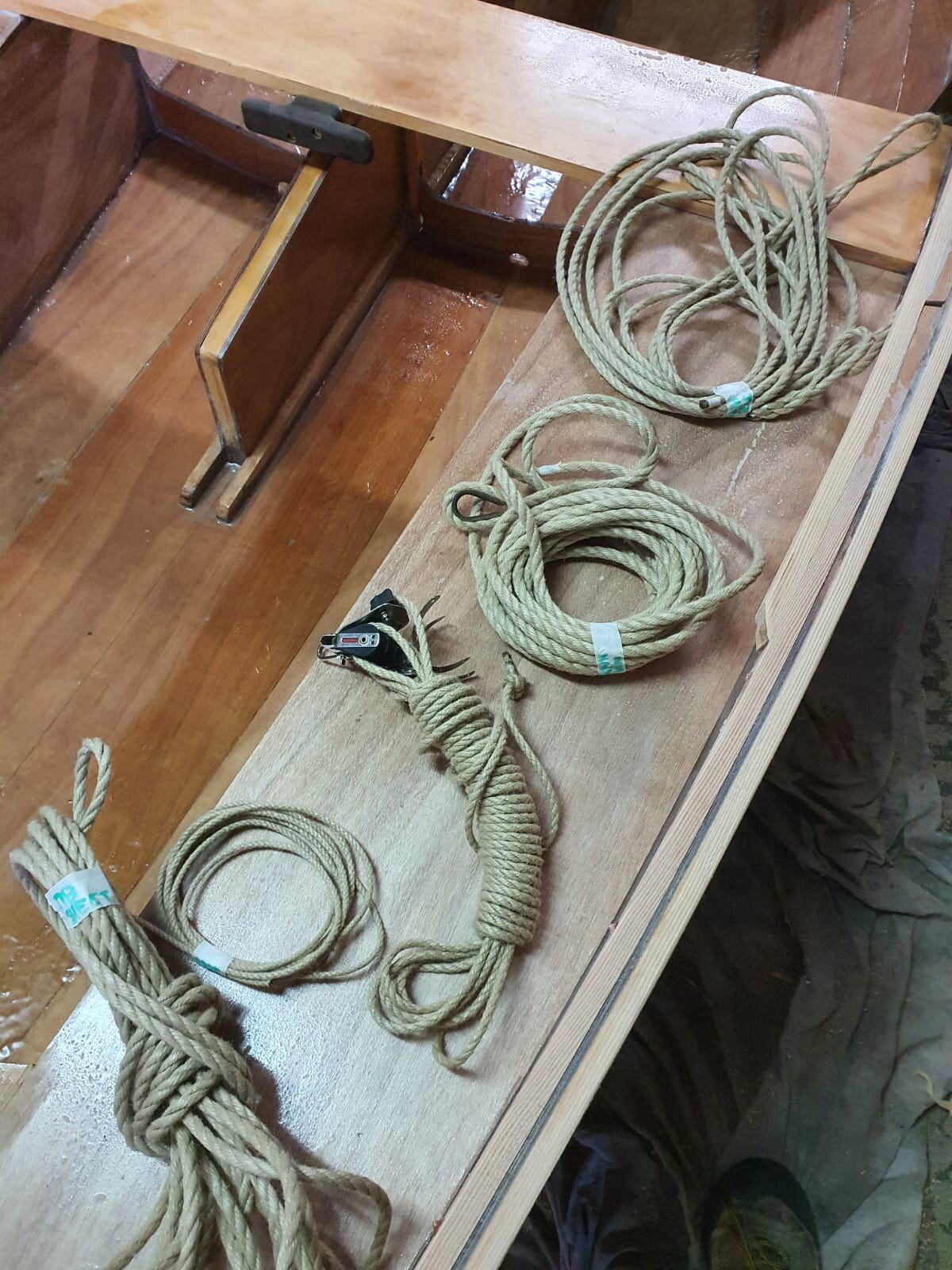
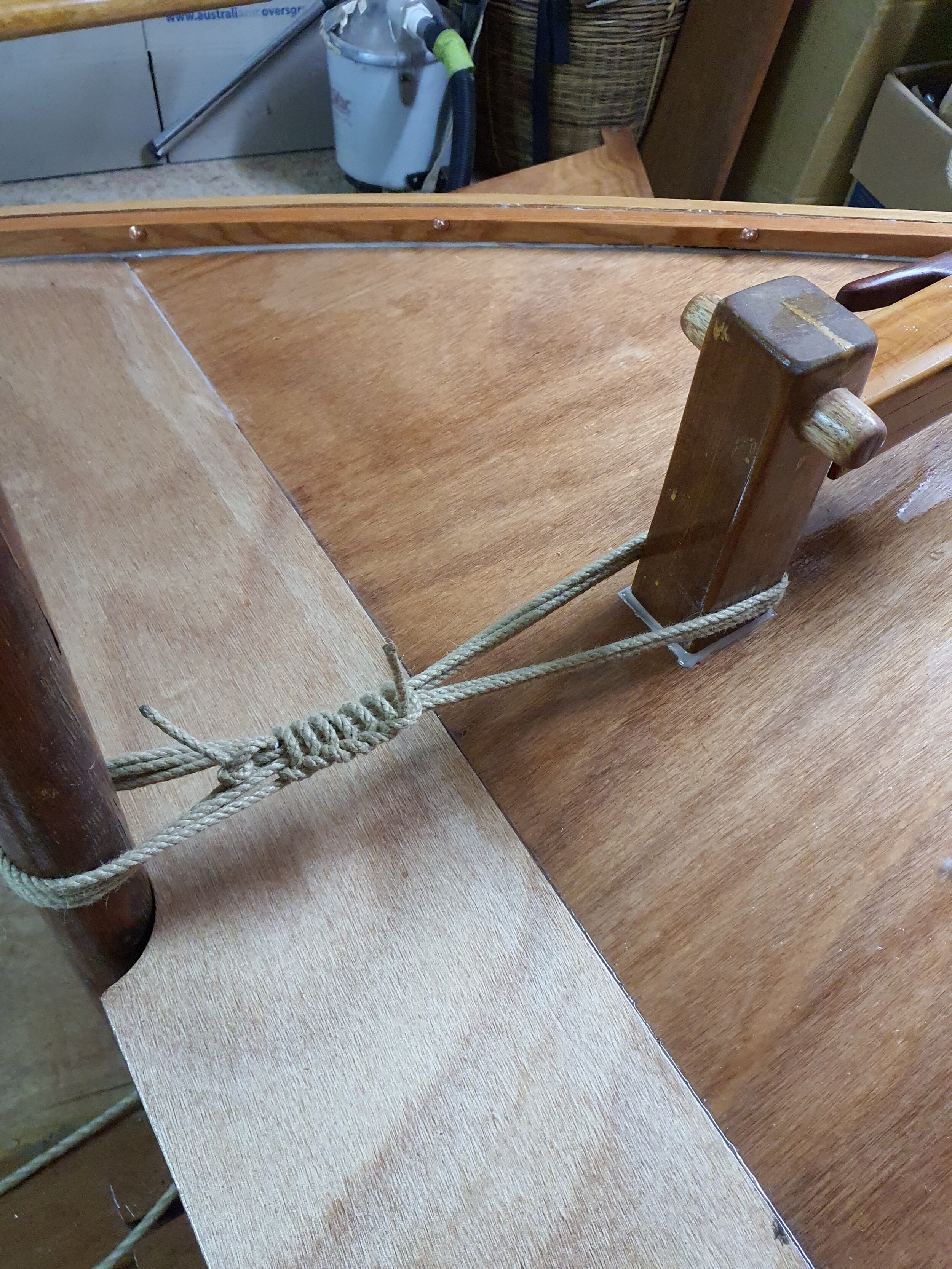
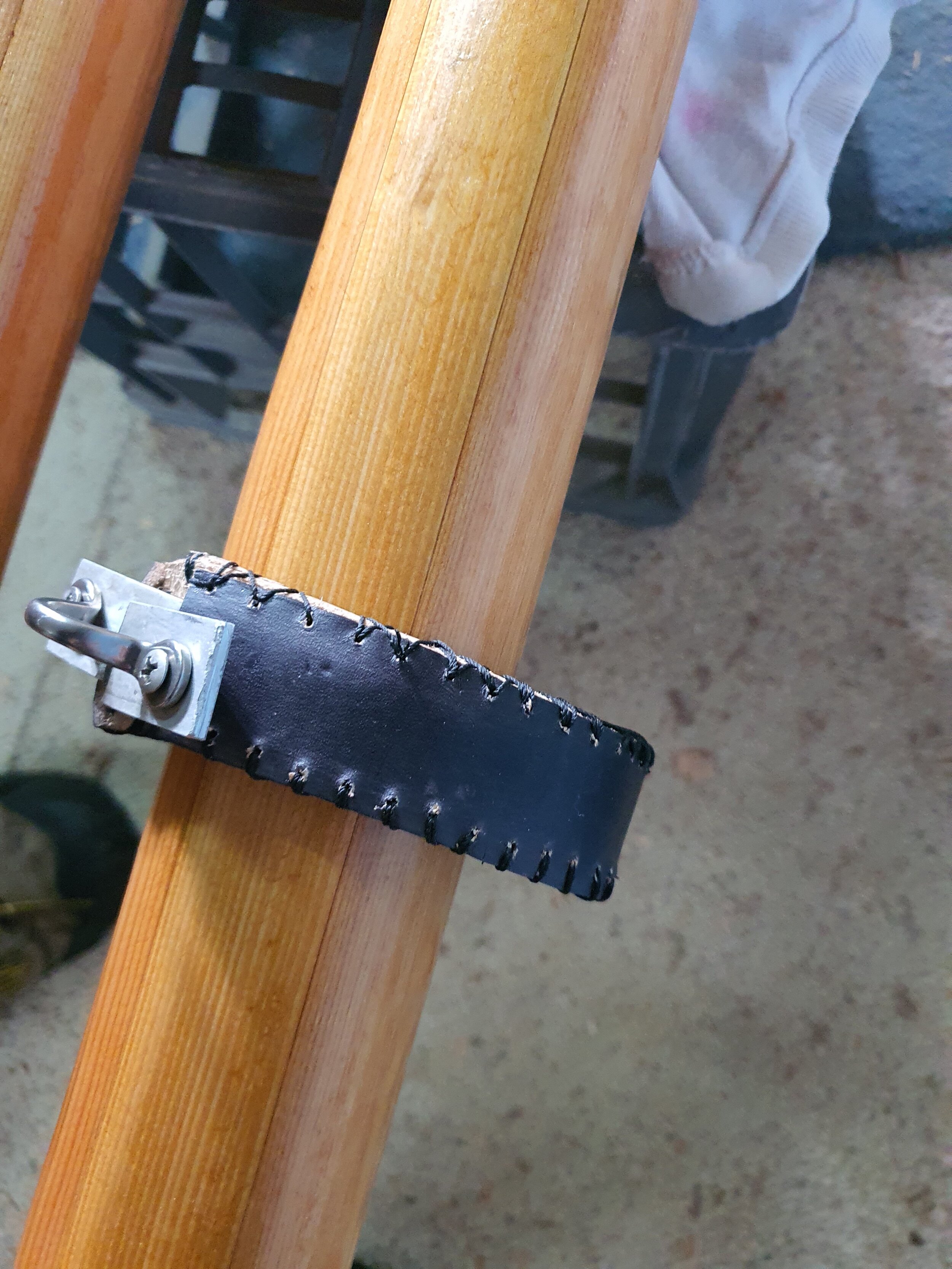
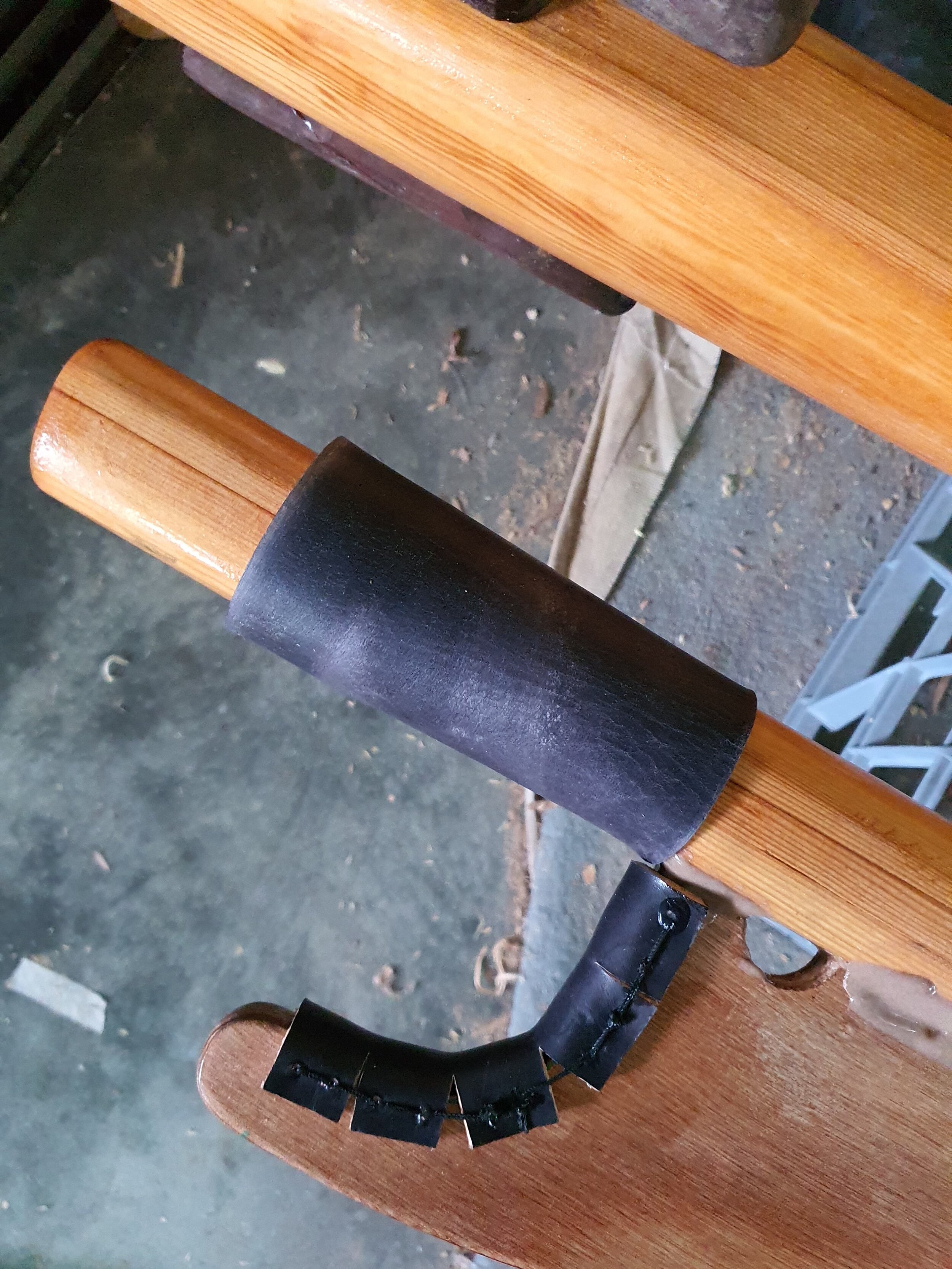
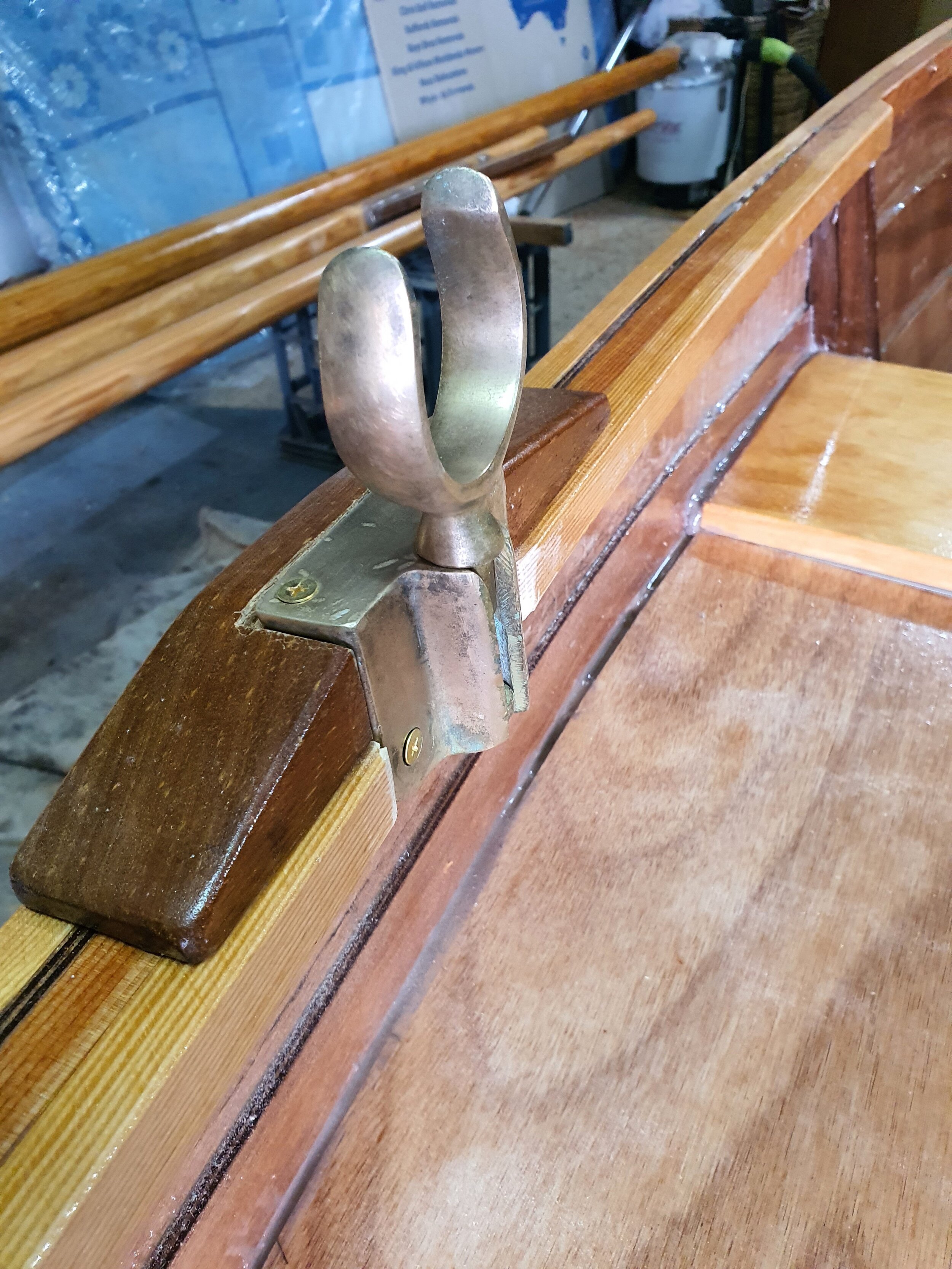
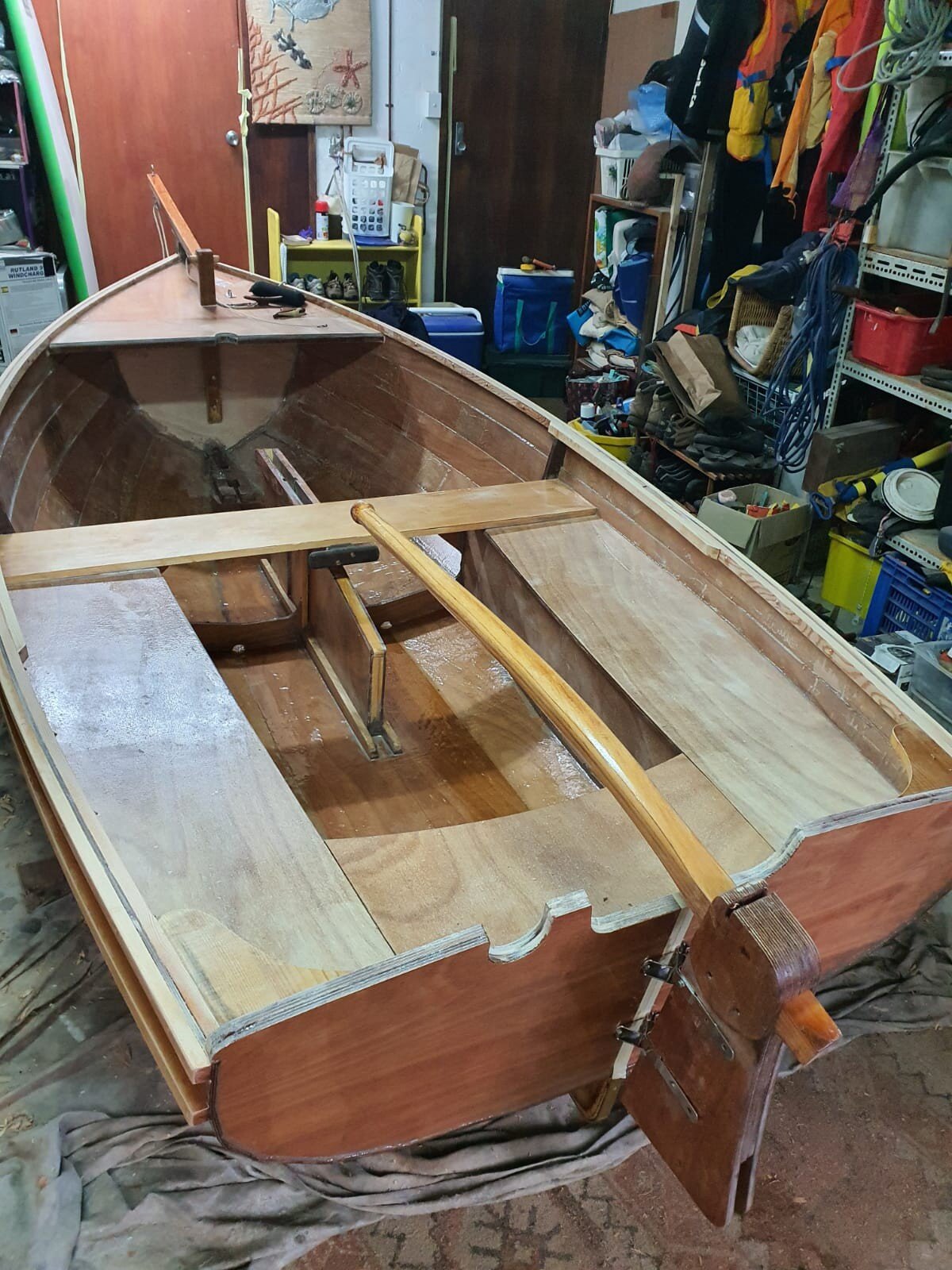
All in all, though, it is close to an ‘as the plan’ construction and it is a very pretty little boat. It is not perfect, but I can’t wait to have some adventures.
Swan River
Harvey Estuary
Bassendean
Martin Chambers describes himself as an author, kayaker and failed biologist. Read more of his writing here